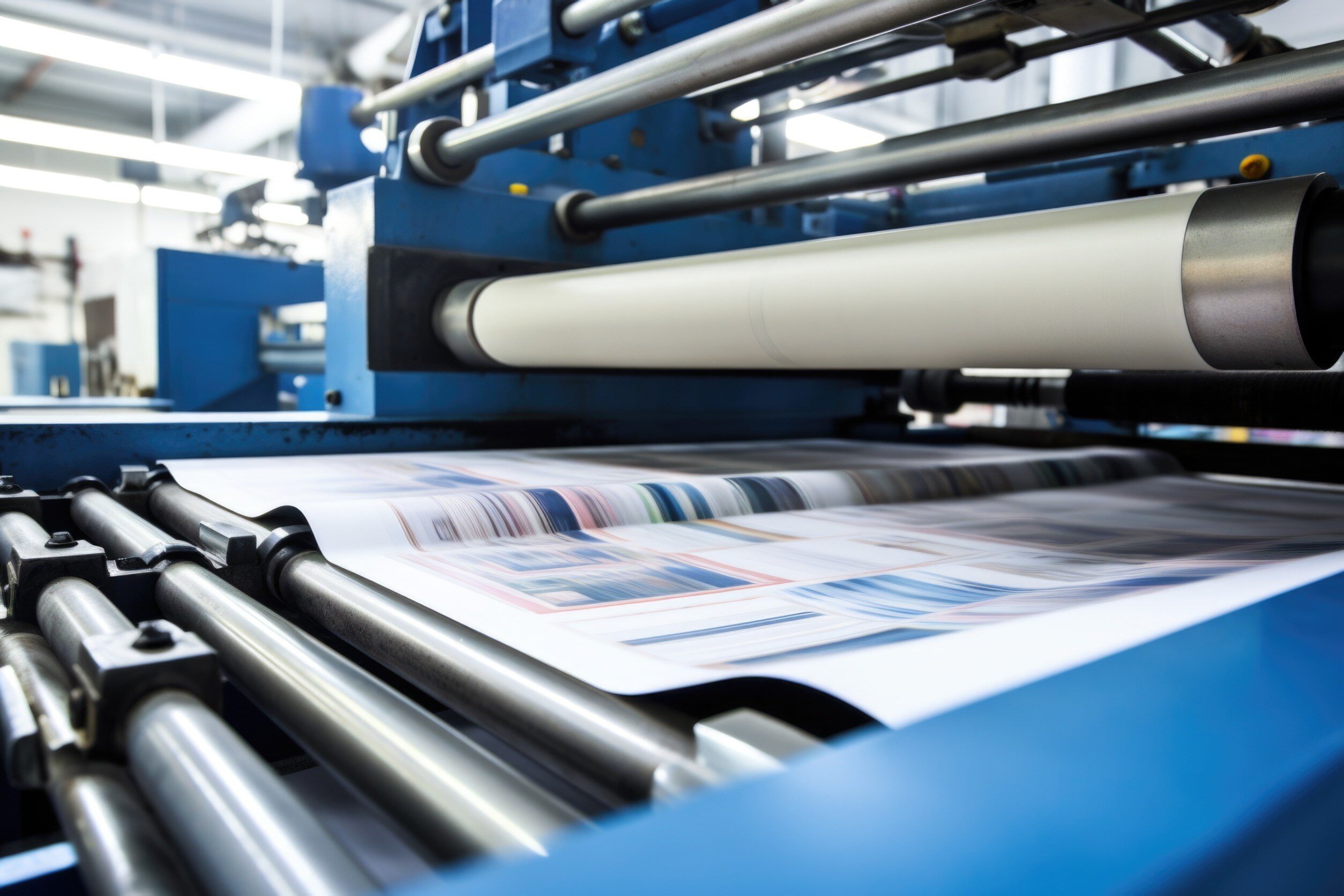
There are several common printing processes used in the production of packaging, each with its own advantages and disadvantages in terms of cost, print quality, flexibility, and applicability to different types of packaging materials.
Here are some of the most common printing processes for packaging:
The technologies used for packaging printing
Flexography: Flexography is a rotary printing method often used for printing on packaging materials such as corrugated cardboard, plastic bags, labels, and films. It is fast, suitable for long runs, and can print on a wide variety of substrates.
Offset: Offset printing is frequently used for folding carton packaging. It produces high print quality and is ideal for packaging with heavy graphic content. However, it is less suitable for flexible materials.
Gravure: Gravure printing is an engraving printing process used for high-quality packaging such as flexible packaging, labels, and plastic films. It can reproduce very detailed images but can be expensive.
Screen Printing: Screen printing is used to print on a variety of materials, including plastic, glass, and metal. It is often used for special packaging or limited editions due to its cost and slower printing speed.
Digital Printing: Digital printing is increasingly used for customised packaging or small runs. It offers great flexibility in terms of customisation, allows quick job changes, and does not require printing plates.
Letterpress: Letterpress is an old printing method that has largely been replaced by more modern technologies. However, it is sometimes used for special prints or artistic effects on luxury packaging.
Inkjet: Inkjet printing is a complementary printing technique. Fast and suitable for customised and small-batch packaging, it is often used for printing barcodes, expiry dates, and other variable information.
The choice of printing method depends on various factors such as the packaging substrate, production quantity, sough after print quality, printing budget, and specific design requirements.
Advantages and Disadvantages of Each Printing Process for Packaging
Each printing process has its own advantages and disadvantages, and the choice often depends on the specifics of the project such as the packaging substrate and production requirements.
Here is an overview of the advantages and disadvantages of the main printing processes used in packaging production:
Flexography
Advantages:
- Fast and efficient for large runs.
- Suitable for a variety of substrates, including flexible materials.
- Relatively low cost per unit.
Disadvantages:
- Generally lower print quality compared to other methods like offset, although this gap is becoming less noticeable with technological advances.
- Requires the creation of plates or sleeves for printing.
Offset
Advantages:
- Excellent print quality, ideal for packaging with complex graphics.
- Suitable for large runs.
Disadvantages:
- Higher cost for small runs.
- Requires time for initial setup.
Gravure
Advantages:
- High print quality with fine detail reproduction.
- Suitable for long runs.
Disadvantages:
- High cost, especially for small runs.
- Complex process requiring the production of engraved cylinders.
Screen Printing
Advantages:
- Suitable for a variety of materials.
- Allows for special inks and artistic effects.
Disadvantages:
- High cost for large runs.
- Slower printing speed.
Digital Printing
Advantages:
- Great flexibility for small runs and customisation.
- Does not require plates for printing.
Disadvantages:
- Higher cost compared to conventional methods for large runs.
- May be limited in print quality compared to other methods.
Letterpress
Advantages:
- Suitable for small runs.
- Unique effect with raised prints.
Disadvantages:
- Less common and less efficient than other modern methods.
- Limited in terms of quality and complexity of designs.
Inkjet
Advantages:
- Great flexibility for customisation and variable data.
- Relatively low cost for small runs.
Disadvantages:
- May be limited in print quality compared to other methods.
- Printing speed can be lower for large runs.
Next step
The choice of printing process will depend on several factors, including production volume, required print quality, cost, needed customisation, and the characteristics of the packaging material. These recommendations are general, and it is essential for manufacturers to consult with printing and packaging experts to choose the best process based on their specific needs.
Take advantage of a complimentary feasibility study for your packaging range by contacting one of our packaging experts on https://www.millergraphics.com/contact/